The growth of the electric vehicle market and the demand for increasingly efficient motors offer significant opportunities for companies like Sitem, which must continue to innovate to remain competitive in a rapidly changing global landscape. This was the premise of our latest interview with Sitem, shared through the voice of its CEO, Eng. Marco Bartoloni.
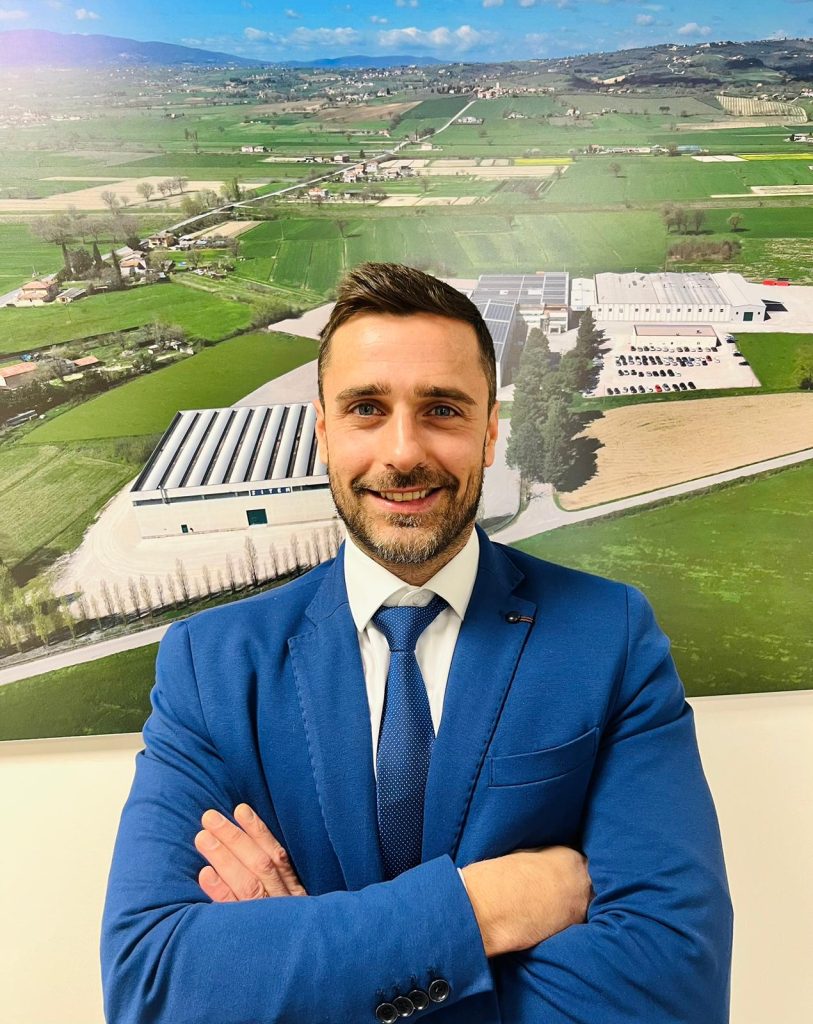
Let’s start with Sitem’s current situation and forecasts for 2025. What is the scenario?
In 2024, the company celebrated its 50th anniversary, coinciding with a major acquisition by the Tempel/Worthinghton Steel Group. Forecasts for 2025 indicate further development of more efficient technologies, such as permanent magnet motors, which could influence the type of laminations required. Some key trends impacting the lamination market include the growing demand for electric vehicles, technological innovation, sustainability, and cost reduction. In short, the ongoing transition to electric vehicles will increase the need for laminations for electric motors. Innovations in lamination production, such as lighter materials processing or bonding solutions to enhance efficiency, will be crucial to maintaining competitiveness. Finally, environmental regulations are driving energy efficiency, pushing companies to develop solutions to reduce production costs while optimizing the use of laminations.
What is your role in this scenario?
Sitem plays an important role in the European electric motor market and together with Tempel will cover the demand of stator and rotor cores for electric motors and generators worldwide. In general, Sitem’s contribution is linked to the supply of stator and rotor cores and diecasted components, which are the heart and the body of any electric motor, including those used in electric vehicles (EVs) and other industrial and electronic applications. We provide high-quality magnetic laminations bonded together with different kind of technologies, as request from our customers. These materials help improve motor performance in terms of energy efficiency and reduce losses due to electrical resistance.
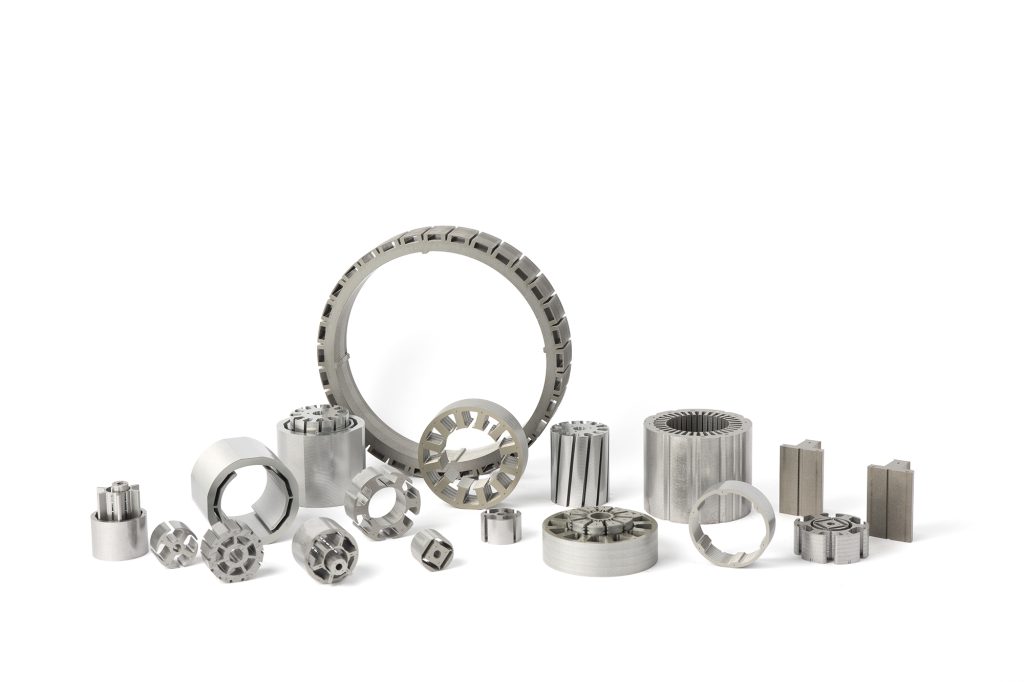
What innovations are you working on?
We are committed to developing advanced solutions for bonding laminations, using multi-dot gluing or full surface backlack solutions with a particular focus on cost reduction processes. To realize that we invest every year from 3% to 5% on research and development of high-performance laminations. The growing demand for more efficient electric motors drives us to continuously improve our product quality by experimenting with new materials and production technologies enabling us to process thickness up to 0,2 mm. This is particularly important in the electric vehicle sector, where performance demands and cost reduction requirements are very high.
Are you focused solely on the automotive sector?
No, we are not. Sitem has a strong background on industrial market which still represents today almost 50% of our turnover. Electric motors are involved in many different applications such as pumps, fans, generator, pump circulator for heating system, logistics, industrial automation, power tools, domotic and renewable energy. This allows us to expand our presence in these areas, becoming a key supplier for various global industrial sectors. We actually process more than 100,000 tons of electrical steel. Additionally, we place great emphasis on sustainability and ecological innovation. With evolving environmental regulations and increasing attention to sustainability, we have decided to optimize production processes to reduce energy consumption.
Can we talk about Industry 4.0?
Absolutely. We have implemented innovative software systems to interconnect our various production plants and monitor production in real-time, improving operational efficiency and product quality. We are also adopting Kaizen, a Japanese philosophy of continuous improvement, to optimize processes and products.
How are you responding to the increasing demand for laminations?
We have undertaken a strategy of expansion and strengthening of our production capabilities. A significant step in this direction was the agreement finalized in December 2024 with Worthington Steel, Inc., through its subsidiary Tempel Steel Company, LLC, to acquire a 52% majority stake in Sitem. This strategic partnership aims to enhance Sitem’s presence in the European market and meet the growing demand for laminations for electric motors, particularly in the automotive and industrial sectors. Integration with Worthington Steel will allow Sitem to expand its customer base and benefit from operational and technological synergies, strengthening production capacity and process efficiency. Moreover, Sitem operates six manufacturing plants in Europe: three in Italy, one in Switzerland, one in Slovakia, and one in France, strategically positioning itself to effectively serve European markets.
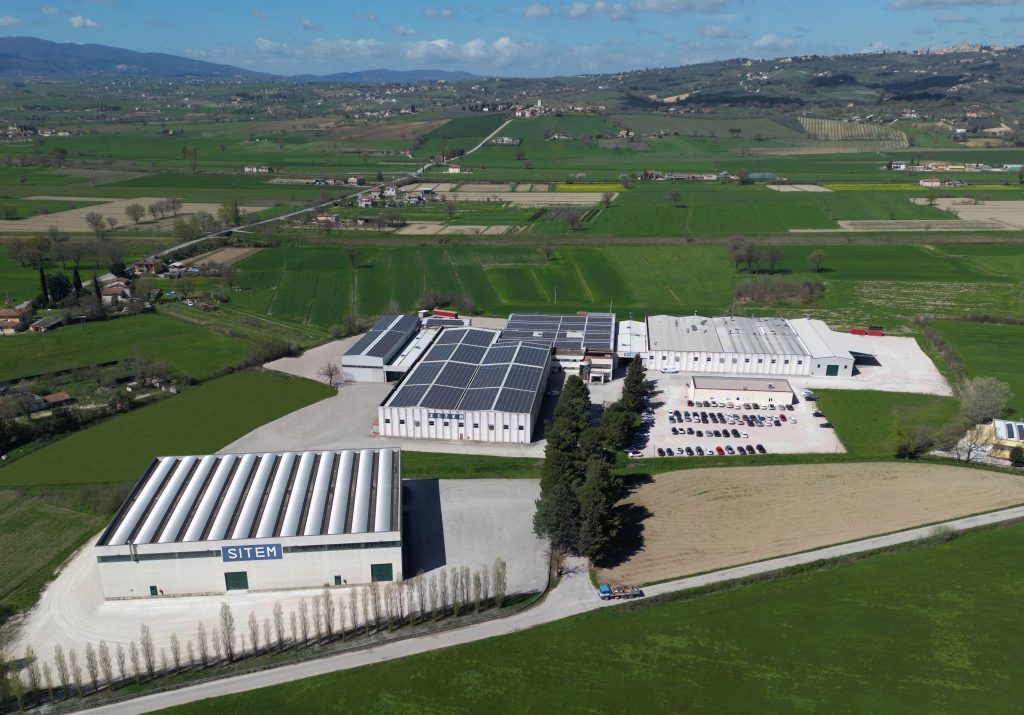
With this overview, how do you manage the supply chain?
Fluctuations in raw material prices and supply chain disruptions pose significant challenges. Sitem must ensure efficient supply chain management to maintain production continuity and product quality in line with technological development and new markets.
Speaking of technological development and new markets, what are the main opportunities for you?
In addition to the already mentioned implementation of Industry 4.0, Kaizen, and expansion into the automotive sector, I would highlight aluminum component die-casting. The company is expanding its expertise in die-casting aluminum parts for motor housings and shields, as well as providing machining processes on die-cast components, thus meeting the needs of various industrial sectors with very high quality level requirement.
by Lara Morandotti