With over 500 international patents and an investment in research and development equal to 7-10% of annual turnover, the Italian company BTSR International continues to innovate to bring value to the winding production sector, where accurate monitoring of wire sliding is essential to guarantee product quality and production process efficiency.
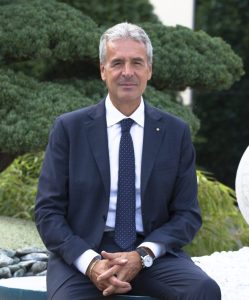
A breakage or malfunction of the wire that is not detected promptly can compromise the entire production cycle, causing defects in the final components and increasing production costs. «BTSR produces sensors for wire control and all our solutions are produced in-house.
Our sensors are mainly used for tension control, wire presence verification and, more recently, we have developed the new IRIDIUM CW/IRIDIUM 3D sensor», explains Paolo Caviggioli, Sales Manager of BTSR International. «Innovation is in our DNA. We will continue to invest in increasingly advanced technologies, to provide our customers with reliable and efficient tools».
New standards for wire defect control: IRIDIUM 3D optical sensor
Caviggioli tells us that IRIDIUM3D represents a breakthrough in the field of wire inspection. The non-contact optical sensor is able to detect defects such as blisters, cracks, diameter variations, lack of enameling, and even missing wire in real time.
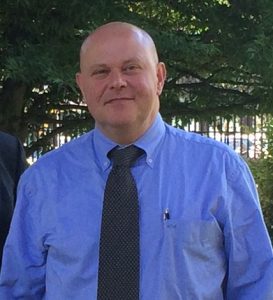
This innovative control system enables manufacturers of electric motor wires to certify product quality by detecting any imperfections and ensuring high standards of accuracy. One of the main uses of IRIDIUM 3D involves wire enameling machines: a coil can stretch for several kilometers and it is essential to verify that each section meets quality standards.
The system is able to record and map defects by specifying the exact spot where they are located. The PC LINK WEB IRIDIUM software therefore allows it to automatically store and classify manufactured coils based on the defects found, assigning them a value between Class A, B, C or D.
«For the first time, wire manufacturers can have a patented optical sensor that combines digital sensors (microcameras), adjusted by ultra-fast analog sensors, capable of analyzing the wire with a 360-degree view, without any direct contact and with accuracies in the order of a handful of microns», Caviggioli points out.
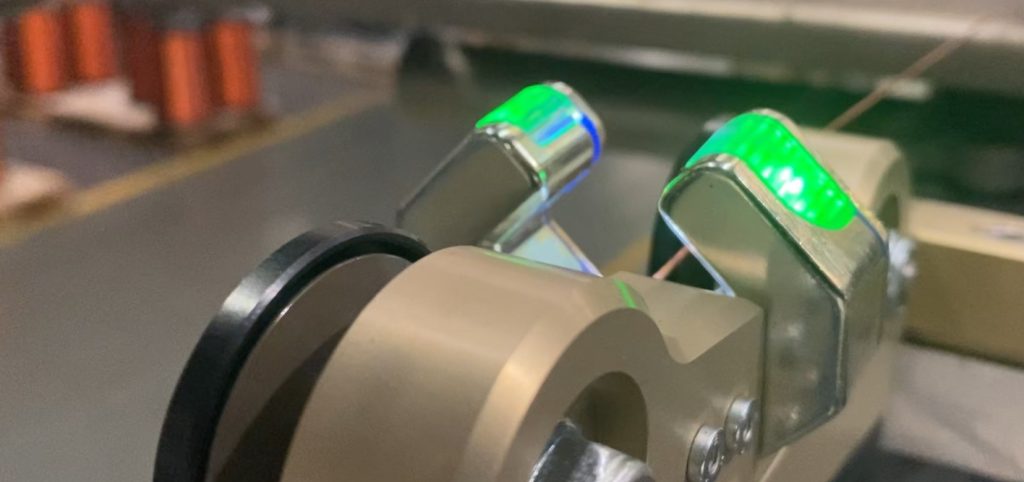
The sales manager says that compared to traditional laser beam-based inspection systems, IRIDIUM offers a complete view of the wire, ensuring accurate and reliable detection of defects. «Among the main advantages I emphasize the certification of wire quality with real-time measurements and the system’s ability to ‘photograph’ and track each defect graphically».
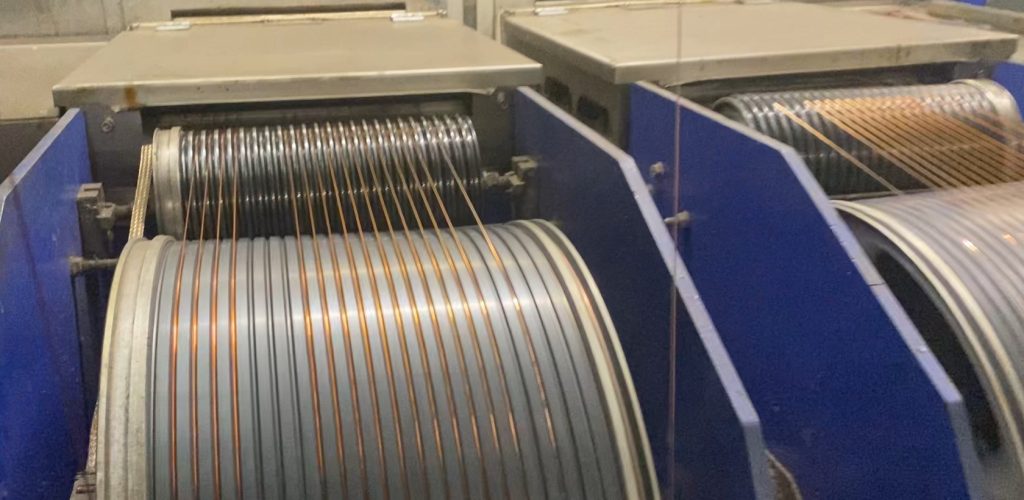
Going into more detail, IRIDIUM 3D is an IP67-certified small sensor that can verify wires with a minimum diameter of 0.1 mm and a maximum of 6 mm, while offering robustness and resistance against dust and adverse industrial conditions. IRIDIUM 3D uses a patented three-dimensional analysis system. «Thanks to our technology, IRIDIUM 3D combines CCD and analog technology to self-calibrate in real time, monitoring the wire regardless of its position», says Caviggioli. This sensor requires no contact with the wire and provides accurate monitoring without altering the voltage or generating impurities.
The MATRIXTOUCH IRIDIUM terminal and the PC-LINK WEB IRIDIUM software allow data to be collected during processing and the wire analyzed to be certified. “The sensor can be equipped with the AIR JET accessory, an automated compressed air cleaning system that can be programmed from the Matrix Touch terminal,” adds Caviggioli.
The importance of software
For advanced production data management, BTSR has developed the MATRIX TOUCH IRIDIUM Terminal, which collects and analyzes information read from sensors. PC LINK WEB IRIDIUM software, which can be installed in a server, collects and stores data from all MATRIX TOUCH terminals.
«Without this software, it would not be possible to certify the coils produced. Each wire can be monitored, generating detailed reports on any defects in the wire», Caviggioli explains. «We designed this software to collect sensor data because without an analysis system, it would not be possible to verify the characteristics of the wire. The software was developed to be installed in the company server». PC LINK WEB IRIDIUM COIL thus allows all information to be stored in a database and enables detailed analysis of each anomaly, providing a snapshot in graphical version for each defect detected.
The software’s main features include real-time monitoring of production parameters, certification of coil quality, predictive defect analysis and process traceability. «The system is compatible with iOS and Android devices. With an intuitive interface, the software allows remote and real-time control of every stage of production, seamlessly integrating into Industry 4.0 processes».
Two-dimensional and non-invasive control
Using patented advanced control methodologies, BTSR has developed a range of sensors capable of non-invasive (touchless) wire monitoring. «BTSR’s CW/IS3F2/TSL sensors are based on the patented Bi-dimensional Image Variation Technique, the result of years of research and development. This technique enables precise analysis of the profile of the wire being monitored, ensuring continuous control of its image variations by dual transmitters over a wide reading area. These electronic sensors measure and detect the state of the wire with extreme precision, identifying abnormal operating conditions or interruptions. «The advanced technology makes it possible to intervene in real time to prevent failures and improve the reliability of the production process», Caviggioli details. The sales manager points out that thanks to BTSR’s patented “Bi-dimensional Image Variation” technology, these devices work optimally even in the presence of machine vibrations, dust and dirt accumulation, water or oil contamination, thus ensuring constant measurement accuracy. In addition to wire slip monitoring, BTSR has developed specific devices for tension control in winding processes. «Maintaining constant tension is crucial to avoid deformation or defects in the finished product. BTSR’s tension devices work in synergy with CW/IS3F2/TSL sensors to ensure complete and automated process control».
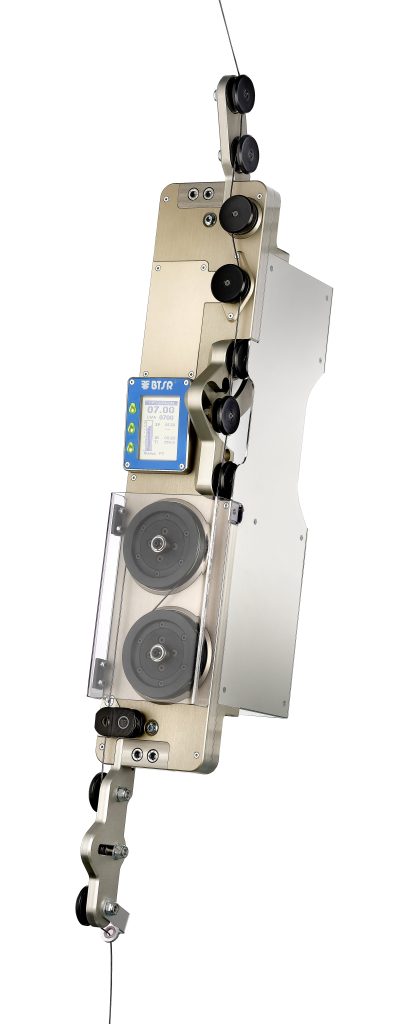
The new MINITRON MEGATRON GIGATRON devices are also based on the new “dual drive system” concept, providing the perfect combination of feed control and control of the length of wire absorbed into the final coiled product. Integrable even on existing process lines, the devices provide the ability (BTSR International patent) to program up to three different wire feed voltage values, without any interface/connection to the coil winder, or up to four different wire feed voltage values during the winding cycle, using two digital outputs of the winding machine. BTSR devices can communicate via EtherCat Profinet Ethernet IP or RS485 for easy integration and communication with PLCs of new winding lines. «BTSR International’s unique, award-winning technology certifies that the windings produced meet stringent parameters for voltage and length of wire absorbed, thanks to two advanced monitoring systems», Caviggioli explains. «Specifically, the first closed loop named “Motor Torque” ensures control of the motor torque, keeping the output wire voltage constant regardless of input voltage variations, while the second closed loop named LWA ensures that the amount of wire wound is always constant by detecting any dimensional variations in the spools, errors in wire measurement or impurities in the wire guide passages».