Inline integrated and automated corrosion protection coating for e-mobility battery housings. Plasmatreat and Linamar: a successful production implementation of PlasmaPlus technology.
Corrosion protection coating for e-mobility batteries
A leading automotive manufacturer was faced with the challenge of significantly improving corrosion protection for battery housings in electric vehicles and efficiently integrating it into its production lines. He recalled a series of tests at Plasmatreat GmbH in Steinhagen, Germany. Thanks to the collaboration between automotive supplier Linamar GmbH and the German atmospheric pressure plasma specialist, it was possible to successfully integrate a plasma coating system into the sophisticated production line for battery housings. This close collaboration combined automation expertise with plasma technology know-how. The result was a more reliable, efficient and environmentally friendly process that significantly increased customer satisfaction and the quality of the end product.
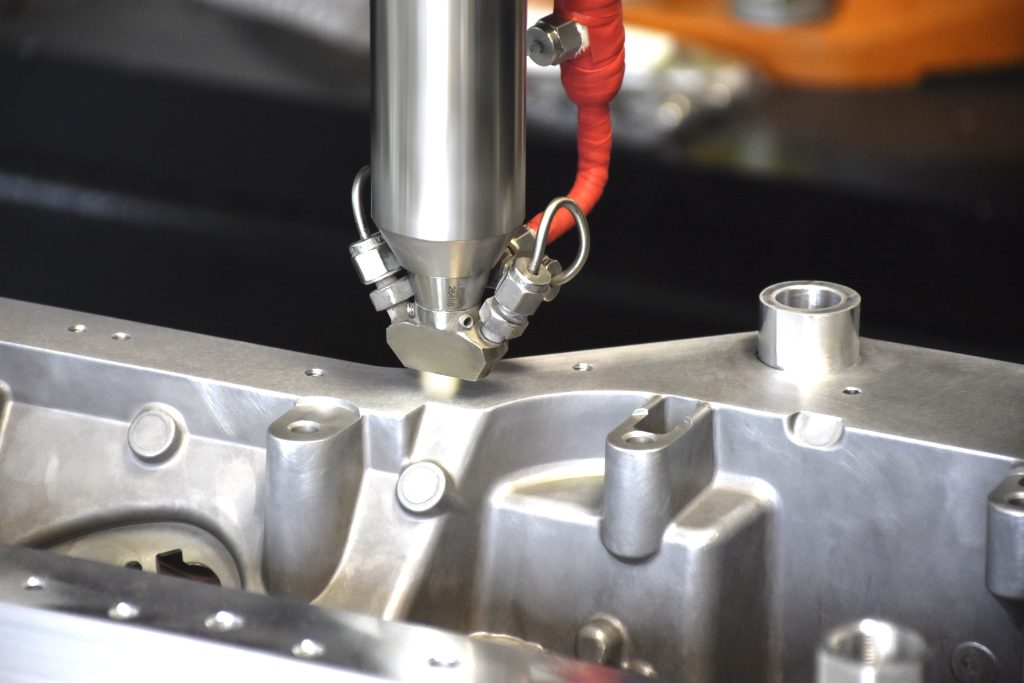
The key role of corrosion protection
Corrosion (infiltration) protection is critical for every automotive and battery manufacturer – reliable corrosion protection measures ensure durability and quality at the highest level. New material combinations such as aluminum or magnesium, which are increasingly used in lightweight construction, are particularly susceptible to corrosive infiltration. Innovative and high-tech solutions are required to ensure the long-term functionality and operational safety of automotive components. Effective corrosion protection plays a key role in improving the quality of components and the overall vehicle, and therefore has a significant impact on a automotive manufacturer’s brand image.
A well-known high-end car manufacturer was open to a new approach in this area. It was looking for a reliable solution for the heart of its electric vehicles, the battery housing, in which the vehicle’s batteries are structurally bonded. Automotive supplier Linamar GmbH was awarded the contract to develop and build this production line. The company is part of the global Linamar Corporation, an automotive supplier and developer of highly engineered and automated production lines with production facilities in North America, Europe and Asia. The group employs approximately 34,000 people in 75 locations worldwide. The Mobility Division develops powertrain, structural and chassis systems, energy storage and power generation systems.
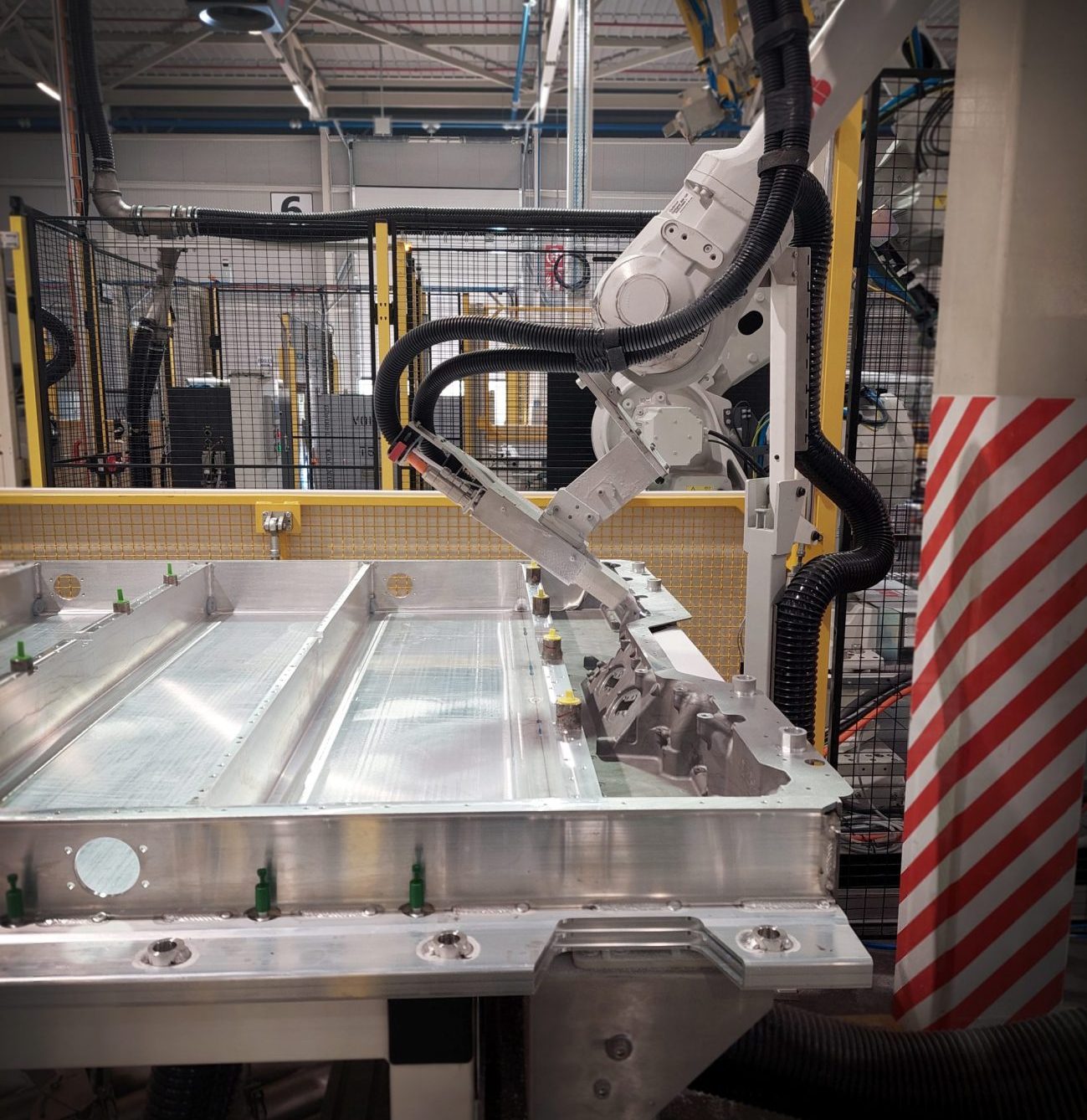
The application problem: protection of the sealing points of battery housings
In a specific application, an inline integrated option was needed to protect the sealing points of battery housings from corrosive infiltration, thereby better protecting the batteries. These housings are made of 90 percent extruded material and 10 percent die-cast material. The die-cast material used has a higher copper content and makes the sealing surfaces particularly susceptible to corrosion. The battery case manufacturer previously used the wax process as an interim solution. This conventional process, which is widely used in the industry, is complex and expensive. This is mainly due to the environmentally harmful chemicals that require complex handling, such as proper disposal. In addition, the process has limited process control capabilities. “Our end customer’s guarantee on the corrosion protection of their vehicles is always very high. The protection should generally last for two decades. This requires process reliability and traceability. The interim solution did not meet these high requirements. So together we looked for an alternative,” explains Joao Esteves, Global Director of Product and Process Engineering Structures and Battery Enclosures at Linamar.
In its search for a suitable process, the customer brought Plasmatreat GmbH to the attention of its supplier. The high-tech company, headquartered in Steinhagen, North Rhine-Westphalia, Germany, is the world market leader for atmospheric plasma systems, which are increasingly being used in the automotive industry, among others. Plasmatreat has developed atmospheric pressure plasma generation with Openair-Plasma and made the process usable on a large industrial scale.
Atmospheric pressure plasma: how it works
Plasma technology is based on a simple physical principle: the application of energy causes states of matter to change. When more energy is added to a gas, it becomes ionized and enters the high-energy plasma state, the fourth state of matter. When plasma with its high energy level comes into contact with materials, the surface properties change, e.g. from hydrophobic to hydrophilic. In industry, atmospheric plasma systems from Plasmatreat are used for ultra-fine cleaning, activation and coating of surfaces. They offer effective solutions to many material problems and are in many cases an environmentally friendly alternative to conventional processes. To operate a plasma system, you need a generator, a PCU (plasma control unit with integrated transformer) and a plasma nozzle. The speed, type and distance of the nozzle head, as well as the intensity of the beam, are precisely adjusted to the surface to be treated and the purpose of the treatment – one of the core competencies of the German high-tech company.
For example, atmospheric pressure plasma can be used to micro-clean metal surfaces to prepare them for a subsequent coating, such as an anti-corrosion coating. Depending on the type of contamination on a metal surface, Plasmatreat’s Openair-Plasma systems use different gases as process gas, e.g. compressed air or forming gas. Openair-Plasma reliably removes wafer-thin layers of dust and residual traces from the production process, such as oil or grease, and prepares the substrates for further processing. The PlasmaPlus process developed by Plasmatreat is used for effective corrosion protection of metall surfaces. It involves the application of an ultra-thin coating that creates functionalized surfaces. A gaseous precursor is added to the plasma beam. In this specific case, an ultra-thin, highly effective glass-like layer only about 300 to 500 nanometers thick is deposited on the metal surface. This silicon-organic coating – called AntiCorr – creates optimal conditions for corrosion protection and the application of sealants. The protective layer significantly improves the wettability of the surface, which increases adhesion and prevents the sealant from corroding. The process has already been extensively tested and has passed standard climate and salt spray tests such as PV1209 and MeKo-S.
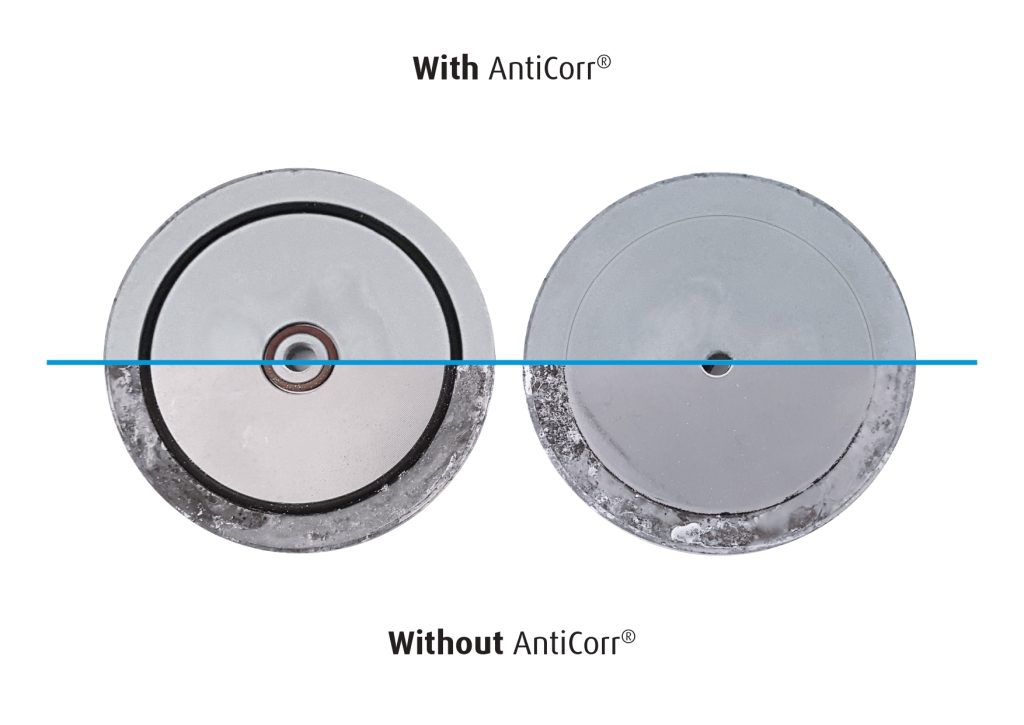
Efficient inline solution for a smooth process
The automotive manufacturer had already used the services of the East Westphalian company a few years earlier to carry out robot-assisted validation tests on coated battery housings. The company was impressed with the results and the plasma specialist’s extensive expertise, particularly in the treatment of extruded profiles. And so, at their express request, Linamar and Plasmatreat began working together. In close partnership, the plasma system was implemented in the production line to coat the battery housing with the PlasmaPlus AntiCorr process. In 2021, the first plasma system was integrated into the Czech plant of the automotive manufacturer. Openair-Plasma is used for ultra-fine cleaning of the sealing surfaces to prepare the housing for the subsequent coating. The AntiCorr coating is then applied. The Plasma Control Unit (PCU) ensures reliable, verifiable and reproducible processes and real-time tracking of process parameters. The PCU combines a variety of control, regulation and monitoring functions. It records and documents critical process data such as current and voltage values directly at the plasma nozzle with the Plasma Power Measurement Module and provides continuous monitoring of plasma generation with the Light Control Module. The Gas Flow Control Module continuously adjusts the flow rate of process gas, while the Pressure Control Module monitors nozzle back pressure and the Rotation Control Module monitors nozzle rotation and the condition of motors and bearings. These functions allow the treatment to be dosed as needed and provide seamless, real-time quality control, ensuring optimal reproducibility of the entire process.
The real challenge: the implementation phase
«The implementation phase was the most challenging part of the project. Among other things, the plasma system had to be optimally adapted to the desired high process speed – a real challenge, but one that we successfully overcame together,» says Joao Esteves. The inline capability of the Plasmatreat systems meant that one of the key advantages of atmospheric plasma technology could be fully exploited. Unlike other processes, plasma systems can be automatically integrated into existing lines. This is an unbeatable advantage in terms of efficiency in industrial production. Compared to traditional processes such as waxing, significantly shorter cycle times can be achieved. The dry plasma process also allows the sealed battery cases to be processed immediately. At the same time, significant logistics costs are eliminated, such as those associated with the space required for component drying. Plasma technology also pays off in terms of material consumption: in the PlasmaPlus process, a maximum of 50 g of the respective precursor is fed into the plasma jet per hour. This makes plasma technology not only more material-efficient, but also significantly more environmentally friendly than conventional surface treatments to prevent corrosion. By eliminating the need for chemical baths, the environmental and health impacts are reduced.
Satisfied customer – to be continued
The new, automated, inline PlasmaPlus corrosion protection process passed the automotive manufacturer’s rigorous tests for resistance to a wide range of environmental influences. As Joao Esteves emphasizes, there is a high level of satisfaction on all sides: «In the joint development of the final process solution for our customer, Plasmatreat has always been very solution and service-oriented». The new system runs well and delivers a significantly improved end product in terms of corrosion protection. As a result, the automotive manufacturer is already planning to install additional systems at its plants in Northern Macedonia and the USA. The cooperation between Plasmatreat and Linamar is also continuing, as Esteves reveals: «We are already working on future projects to further develop the use of plasma for the next generation of battery casings.»
(by Omar Falconelli)