Bearings play a key role in the operation of rotating components and, therefore, of systems with rotating parts. As well-known, they allow supporting radial and axial loads and they allow managing high torques due to low internal frictions in case of optimal lubrication. Among the mentioned systems, in the automotive field we can find a broad range of bearings purposely designed to carry out the expected function suitably. In this ambit, among the main subsystems where bearings are used, we find the transmission organs connected to the motor, the wheels, the steering, the pumps and many other services linked to main components.
Bearings assure optimal performances through the correct selection of materials, manufacturing technologies, optimization of geometries, sealing and lubrication solutions, besides taking the specific features of the application into account. State-of-the-art vehicles, in particular, are provided with high standards of passenger’s comfort that have an impact also on the better performances of bearings, especially in terms of vibration and noise.
Bearings for the automotive sector of the future
The main research areas related to the technology of bearings currently concern the improvement of their reliability in time, the ideation of manufacturing versions with high power density, the development of integrated functions (such as the monitoring), the reduction of friction, the development of performing sealing and lubrication solutions, the integration of special sensors for specific applications.
Modern electronic solutions, through sensors integrated in bearings, play a critical role in the monitoring of the vehicle’s health status. The automotive industry in particular is addressing CASE (connected, autonomous, shared and electric) solutions. The most recent vehicles are conceived at systemic level to maximise their activity time, according to the car sharing logic.
The main research and development trends of the sector concern:
- the environmental sustainability;
- the shared mobility;
- autonomous vehicles;
- the interconnection and the exchange of information among vehicles, or between vehicle and IT infrastructures;
- the electrification of the kinematic chain.
We can generally notice that cars use a higher number of electronic components than in the past, thanks to new functions introduced. Therefore, the vehicle use optimization and the monitoring of the health status in real time become increasingly relevant.
The evolution of automotive powertrain technologies also exerts an impact on critical components/subsystems like bearings. Modern vehicles’ bearings are much more refined and technologically superior than conventional bearings, offering manifold additional functions if compared to the typical primary functions of conventional bearings.
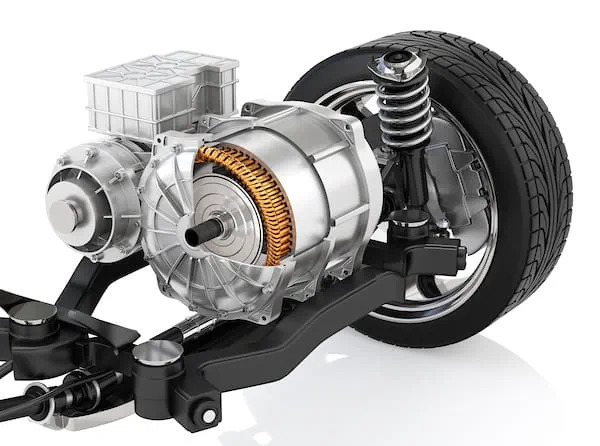
Role of bearings in power transmissions
Let us start from the bearings associated to the motor group. In recent cars, these bearings are no longer used just to satisfy the primary functions, that is to say supporting the operational load acting on the shaft, to facilitate the torque transfer and to reduce the friction, but they are used for integrated functions, too. These bearings, for instance, can detect the rotor positioning, or they interact with devices for the signal transmission with the motor.
Moreover, additional functions include the reduction of noise and vibrations of the whole system and the stiffness correction of shaft systems. In any case, even with these additional functions, it is always necessary to take fundamental design requisites into account, such as the light weight, the space constraints and burdensome operating conditions that include high temperatures and speeds, impossible lubrication restoring and long maintenance intervals.
Therefore, it is clear that the role of bearings is changing. Thinking of electric vehicles, they impose new operation requisites, for which very reliable and performing bearings are demanded to reach the desired specifications. From the role of support component of the shaft, bearings become a system solution for the achievement of new performance parameters.
The bearing plays a central role in the monitoring of the health status of the system where it is mounted, for instance analysing the vibrations acting on this component it is possible to identify, to foresee and to prevent potential failures proactively. Furthermore, significant progresses in ICT technologies, in electronics and in the sensor miniaturization facilitate their integration inside bearings to optimise many other foreseen functions.
Electric battery motors operate at much higher rotation speeds and temperatures. In an electric system, the lubrication of rotating parts is one of the primary challenges. For this reason, the absence of maintenance, together with a silent operation, is one of the technical requisites most demanded for bearings. Therefore, the design of bearings for electric vehicles must satisfy the criteria of high-speed operation, high-performance lubrication and soundness of seals to assure the lubrication of rolling elements and to protect rolling raceways against external contaminations.
Electric powertrain groups, obviously with particular reference to motors, operate with higher accelerations and decelerations than thermal engines and then bearings must be able to manage these performance requisites.
An unsuitable design of bearings can cause functional and reliability problems of the system, which can result in failures or at least in reductions of the service life duration of the powertrain group or of service components of the system. Bearings’ loading capacity as well must be higher than in the past, in consideration of the bigger power of motors and of the availability of a narrow space owing to the minor weight at disposal of the vehicle’s mechanics to compensate the weights of the battery pack.
The bearing design, starting from the geometry, from the selection of materials and from the manufacturing process, plays a fundamental role to obtain higher loading capacities in a small-size envelope. The small sizes of bearings obviously facilitate the reduction of the system’s overall weight.
We ca state, in brief, that bearings play a “mission-critical” function in forefront automotive powertrains. A deeper understanding of the expected applications and functions plays a crucial role in the design of suitable bearings for state-of-the-art automotive systems.
In a conventional transmission system of a vehicle, with internal combustion engine, bearings have relatively different technical requisites, they are well lubricated and they have comparatively lower operation speeds. The figure 1 shows the configuration of an electric vehicle’s transmission system; here, although the transmission layout is simpler, the technical specifications and the performance requisites with which bearings must comply may be stricter.
Bearings for automotive subsystems
Today, the research in the field of electric battery powertrains prevailingly focuses on solutions aimed at increasing vehicles’ autonomy and at shortening charge times. Such requisites, if transferred at the development level of the electric propulsion system, determine further specific requisites, such as:
- High speeds of the electric motor to allow decreasing the mass of the electric motor
- Efficiency optimization along the entire kinematic chain
- Mass reduction through lightened components
- Low friction of the wheel’s bearings to increase the vehicle’s autonomy.
To satisfy the above-mentioned requisites, the development of bearings takes a key role.
The specific function and application of a subsystem with rotating organs obviously influence the selection of the bearings installed in its interior and their performances, too. Therefore, the accurate understanding of the bearing’s work environment is essential. Depending on the application, in fact, the designer will have to impose different technical requisites that bearings are called to satisfy, still in view of the optimization of the entire system’s performances.
We are hereunder reporting an exhaustive overview of the subsystems in automotive ambit and of the characteristics demanded to the respective bearings with relative criticalities.
Bearings for the transmission system:
- High axial and radial load capacity
- Small overall dimensions and weight
- Low friction
- Reduction of NVH (noise vibration harness, a measuring unit of the vehicle’s comfort)
- User-friendly assembly, disassembly and regulation
- Compatibility with lubricants
- More tolerance to the most demanding operating conditions (variations of load and speed, temperatures and contaminations).
Bearings for the motor group:
- Operation at high temperatures
- Variable loads and speeds
- Challenging operating conditions connected for instance with a high contamination risk
- User-friendly assembly and disassembly.
eMotors bearings:
- Elaborate arrangement of bearings
- Management of high and variable speeds/loads
- High operation temperature
- Low NVH (noise vibration harness) and low friction
- Absence of maintenance and good sealing performances
- Management of accelerations and decelerations in operating conditions
- Tolerance to the electric current dispersion.
FEAD bearings
- Capability of reaching higher speeds
- Management of accelerations and decelerations in operating conditions
- Low friction
- Small overall dimensions and weight
- Operation at higher temperatures
- Operation in absence of maintenance (better sealing performances).
Bearings for the wheel group:
- Motion precision
- Light weight, high stiffness and stability
- Reduction on non-suspended masses, which shares in the improvement of the driving dynamics
- Absorption of external forces
- Long duration, low maintenance, resistance to corrosion
- Sustainable solutions with low environmental impact, also concerning the disposal phase
- Thermal stability
- User-friendly assembly/disassembly.
Bearings for the steering system:
- Low friction torque
- Relatively high stiffness
- Low wear rate.
Bearings for the suspension system:
- Low-friction and distortion-free motion of the shock absorber spring while steering, allowing a smooth movement as response to the road conditions
- Operation without self-aligning torque
- Bodywork insulation from the noise generated on the road.
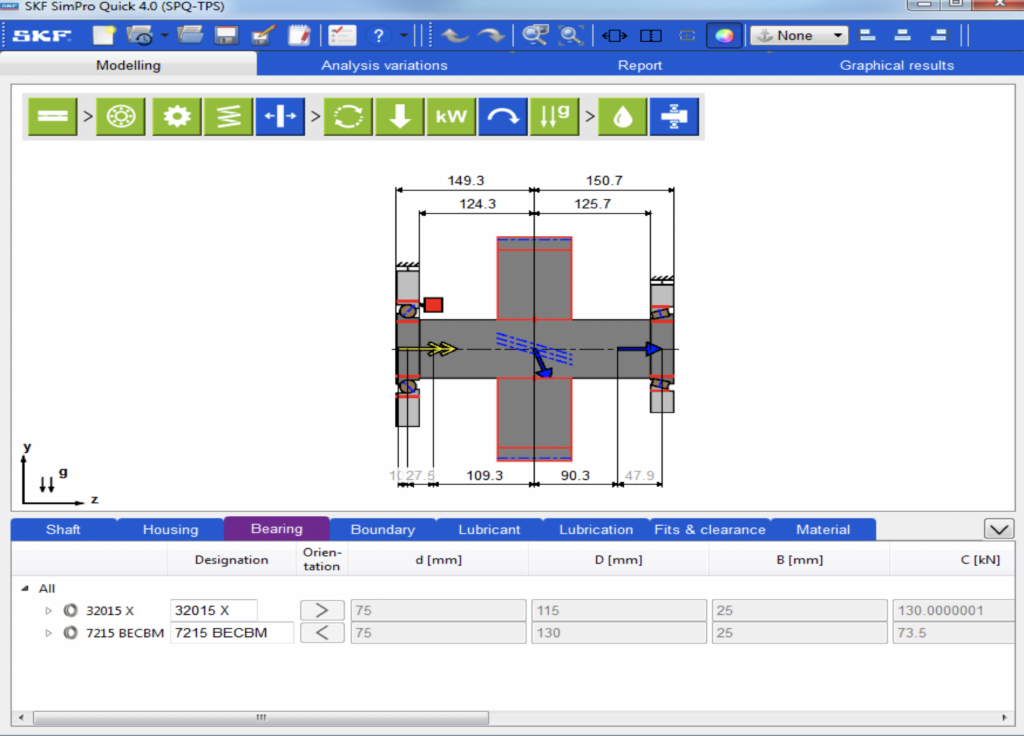
Digital models for systems with bearing
To appreciate the importance of assisted-design software systems, we are considering a practical case of an OEM that detects anomalous vibrations in its car just after the production. These vibrations can be quantified, but the necessary information to determine their impact on the bearings’ duration are missing. With the use of an analysis software, the producer can now simulate the vibrations measured inside a digital model. This allows a complete investigation of the bearing’s performances as response to vibrations, like for instance assessing the effects of rotating elements’ impacts on the bearing’s structure, or analysing the forces transmitted to optimize the duration of the cage.
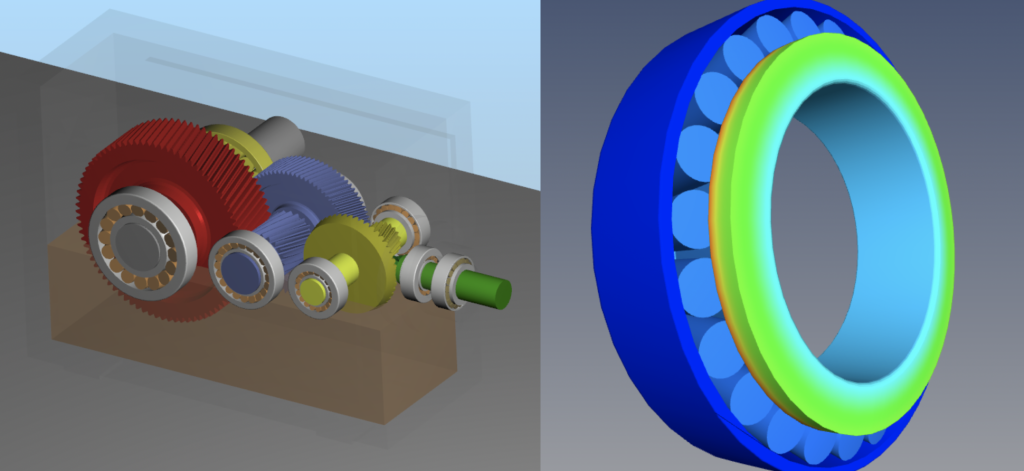
Some suppliers make available some simulation software tools for bearings, suitable for different development phases, from the initial design of single components to the complete sizing of complex machinery with internal analysis. A first approach of software-assisted design is focused on single-shaft systems. Here, the software allows processing shaft geometries and parameters, like the arrangement of bearings, of toothed wheels, of thicknesses, of elastic elements and other components. The designer can simulate the system, assessing its performances after the changes made and forecasting the bearing’s fatigue strength, in addition to operating conditions that might cause its malfunction. This kind of software can identify damages inside the bearing hardly detectable with conventional duration calculations. An example of entry-level software for the design of bearings is SKF SimPro Quick, characterized by a drag-and-drop interface for the addition of components and the visualization of the rotation of rings and of its stiffness.
An advanced software permits to carry out analyses on systems with multiple shafts to obtain detailed models. It enables, for instance, the mass-simulation of virtual reduction gears and other similar systems. In this context, the software functions include
- The analysis of the interaction among kinematically connected shafts;
- The assessment of the characteristics of constraints and of supports in various configurations;
- The importance of CAD OEM or customized components for a more accurate simulation;
- The thermo-structural analysis to evaluate the overheating of the components in operation.
An example of such software is SimPro Expert (figura 3). Even more advanced are the software specialized in the simulation for the sizing and the selection of bearings, such as for instance BEAST (bearing simulation toolbox) software by SKF (figure 4).
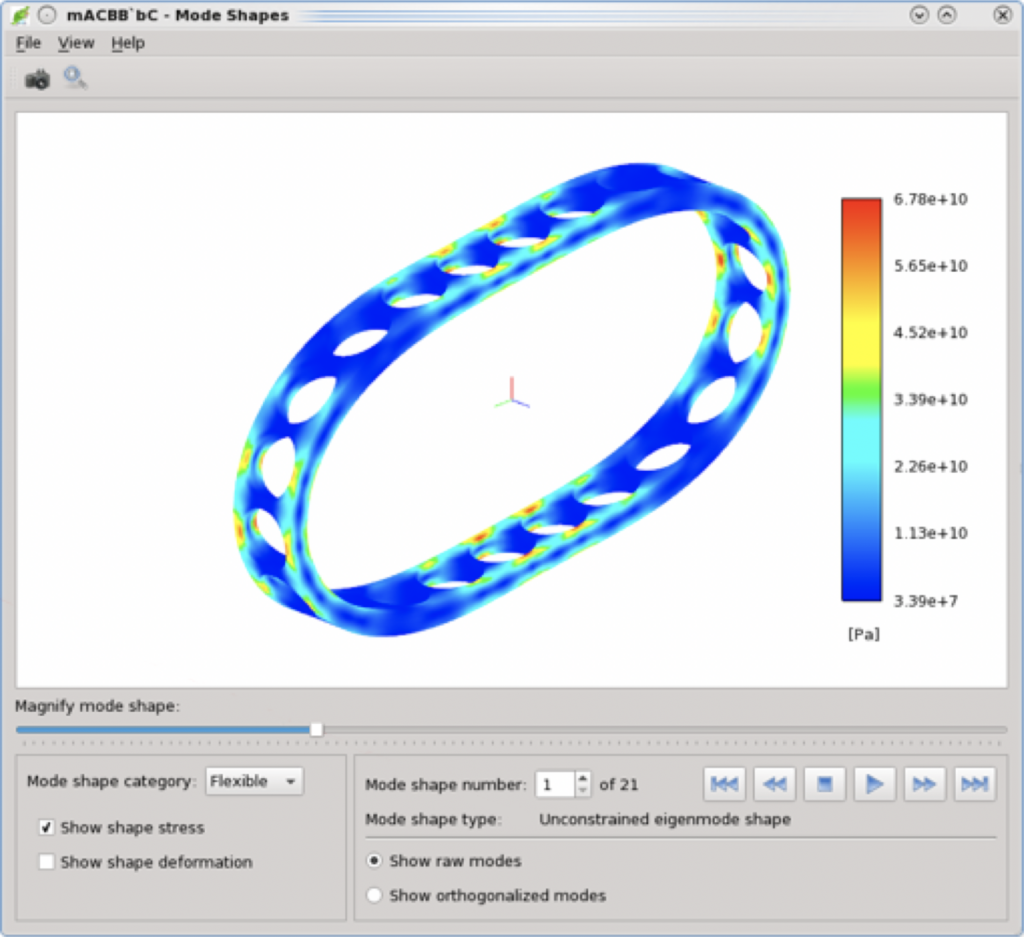
These tools are often developed by the producers themselves of bearings and offer more detailed results than general-purpose software. They allow, for instance, studying in-depth the analysis of the contact between the bearing’s rolling bodies and rings, considering also factors such as the rollers’ bending and inclination. Moreover, bearing manufacturers can provide detailed information about the cage that retains the bearing’s rolling elements, including the dynamics of the interaction between the cage and balls or other rolling elements.
Market prospects
The global market of bearings for electric vehicles, estimated as amounting to 5.27 billion dollars in 2023, is expected to reach 64.73 billion dollars by 2032, with 32.14% CAGR during the considered forecasting period (figure 5).
In recent years, a significant rise of the demand for bearings has occurred all over the world. Data are in line with the fast expansion of the demand for electric vehicles. In 2022, the global sales of electric vehicles reached in fact around 10 millions. However, it may be difficult for manufacturers to suit such a rapidly ascending demand, since the vast majority of bearings developed for conventional vehicles is not suitable for electric vehicles. Some specific modifications must in fact be made in design phase, concerning some key requisites such as: speed, safety and loading capacity.
When conventional bearings are used in electric vehicles, they show a drop of their service life by around 30%. Such reduction can be ascribed to the particular operating stresses imposed by electric vehicles. Electric vehicles’ bearings, for instance, are subjected to an approximately 20 %-higher temperature range versus the one met by bearings for ICE vehicles. Such increment is mostly connected with their proximity to the electric motor and to the high rotation speeds they undergo. Consequently, it is necessary to reevaluate the material composition and the kind of lubricant selected. When we refer to the speed and to the load dynamics, a significant 85% of electric vehicles operate at higher speeds than conventional vehicles. This operating characteristic demands for bearings able to manage higher speeds and axial loads. Producers and OEM (original equipment manufacturers) are then redesigning and engineering the bearings for electric vehicles to improve their duration and power density, which is essential to avoid premature sudden breakdowns.
In terms of materials, still today steel holds the bigger market share, a trend that is expected to persist until 2032. In 2023, steel bearings constituted 40.8% of the market, with projections that show a marginal drop at 40.7% by 2032. Its role proves to be fundamental in the components and in the rings of roller and ball bearings, satisfying the growing demands for performances and speeds in powertrain groups, in particular in electric motors.
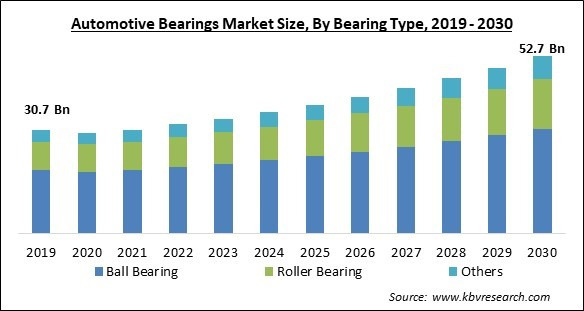
(source: www.kbvresearch.com)
Electric motors are made up by numerous parts, such as bearings, which are the most exposed to electric malfunctions, with concerns about the longevity of power supply systems. An electric damage to bearings represents a not easily identified problem.
The erratic nature of inverter-induced shaft voltages, which tend to follow the path of least resistance, means that solutions like insulated motor bearings could simply redirect the damage to other components, including gearbox or wheel bearings. It is interesting to notice that also the bearings of the internal combustion engine of a hybrid vehicle may have to deal with such criticalities when the vehicle shifts to the electric modality.
Therefore, the global market of bearings for electric vehicles has started witnessing a significant growth of the demand for conductive bearings, as well as for ceramic bearings, which act as insulant. Hybrid bearings, integrating ceramic balls, represent an innovative solution and, despite higher costs, the advantages include a 40%-lower density than steel, a higher performance of these bearings in withstanding higher temperatures and prolonged service life. A substantial 70 % of electric vehicle manufacturers now gravitate towards hybrid ceramic bearings.
Besides the criticalities previously reported, it is then worth reminding that electric vehicles intrinsically have a more silent operating profile than internal combustion vehicles, with the need of low-noise bearings. Besides, lubrication solutions for electric vehicles diverge from those of conventional vehicles. It is estimated that the vast majority of electric vehicles is supporting the use of special lubricants to contrast the premature wear.
The motors of electric vehicles are expected to reach even 15,000 revolutions per minute (rpm), in contrast with just 8,000 rpm of internal combustion engines, with most of cars that reach approximately an average value of 6,000 revolutions per minute. The higher number of revolutions not only enhances performances but it also eliminates the need of heavy and expensive transmissions. However, this imposes rigorous quality expectations on all the components of the powertrain group. Vehicles’ bearings undergo enormous stresses and wear, depending on their use. They must withstand significant centrifugal forces, at the same time avoiding a self-induced heating caused by the fast rotation. In addition to bearings, designers must also take the vehicle duration into account, which must remain reliable on long distances and in future years.
Currently, the advanced tools of Industry 4.0, like the sensors applied to automotive components, offer information about performances in real time and they can be input in monitoring systems. The smart IIoT-compatible bearings rank among these innovations. Such bearings are provided with skills of self-diagnosis and forecasting of imminent problems.
Being at the core of rotating mechanisms, smart bearings can provide precious data about aspects such as the detection speed, the direction and the various forces that influence them.
Smart bearings are used to collect and to transmit information concerning the powertrain group’s conditions. Bearings’ vibrational models, for instance, can offer information about potential problems of the powertrain group and even provide data about the use and the condition of the ground.
Conclusions
Generally, the designer starts the selection and the sizing of bearings by browsing the general indications provided in the supplier’s catalogues. These indications are based on consolidated theories, of both statistical and analytical and experimental kind. However, due to more specific requirements especially connected with the state-of-the-art automotive industry, it is consolidated praxis to use dedicated calculation and simulation tools. Bearings’ simulation software offer notable advantages to the designer in several sectors, such as precisely the one of vehicles, but also of service systems (like pumps and compressors), wind energy, mining, aerospace and many others. The main highlight is the access to more information and a higher control of the most refined details of the application. Design software allow working more rapidly, shortening the time dedicated to tests and, consequently, development costs. Through the software, finally it is possible to define different design variants simultaneously and then to identify the most efficacious one in technical and economic terms.
(by Giorgio De Pasquale, Politecnico di Torino, Department of Mechanical and Aerospace Engineering, Smart Structures and Systems Lab and Elena Perotti, senior data analyst