The emerging technologies in the field of electrical machines are deeply transforming the mobility and energy sector, with a growing emphasis on innovation, optimization and use of the artificial intelligence (AI). Synchronous reluctance machines, permanent magnet motors and externally excited machines are benefitting from advanced solutions such as the optimized cooling and automatic learning algorithms for the forecast of losses and the design of more efficient components. In this article, we are illustrating a survey of interesting innovations in terms of design, AI integration for the optimization of motors and the emerging methodologies that are revolutionizing the sustainability and the efficiency of electrical machines, presented at ICEM (International Conference on Electrical Machines), which was held last September 2024 at Turin Polytechnics.
The role played by AI in the optimization of electrical machines
In the last decades, the evolution of electrical machines has undergone a deep transformation, with an ever-rising focus on innovative technologies, the process optimization and the artificial intelligence (AI) integration. Industry has made great strides in the optimization of machines such as induction motors, synchronous reluctance models and permanent magnet machines. The integration of AI and of automatic learning techniques has allowed speeding up design processes and improving efficiency and performances, with significant benefits in terms of environmental sustainability and cost reduction, too.
One of the primary progresses in the optimization of electrical machines is represented by the use of the artificial intelligence and of automatic learning algorithms. The multi-objective Bayesian optimization (MOBO), for instance, is applied to squirrel-cage induction machines to improve the design process significantly. The complexity of the necessary simulations to optimize electrical machines is one of the main hindrances. In the past, the optimization process needed numerous simulations of the Finite Element Analysis (FEA), which imply long calculation times and high costs. The integration of predictive models based on the automatic learning, such as the Gaussian process regression (GPR), has permitted to reduce drastically the number of necessary simulations, improving the rapidity and the efficacy of the design process.
By means of GPR models, it is possible to foresee the performances of an electrical machine with a low number of training samples, which allows identifying quickly the best candidates for the optimal design. In induction motors, for instance, the optimization process focuses on parameters like the electromagnetic efficiency, the torque ripple and the machine cost, researching a balance among these variables. This approach allows obtaining higher performances, meanwhile decreasing development costs and time.
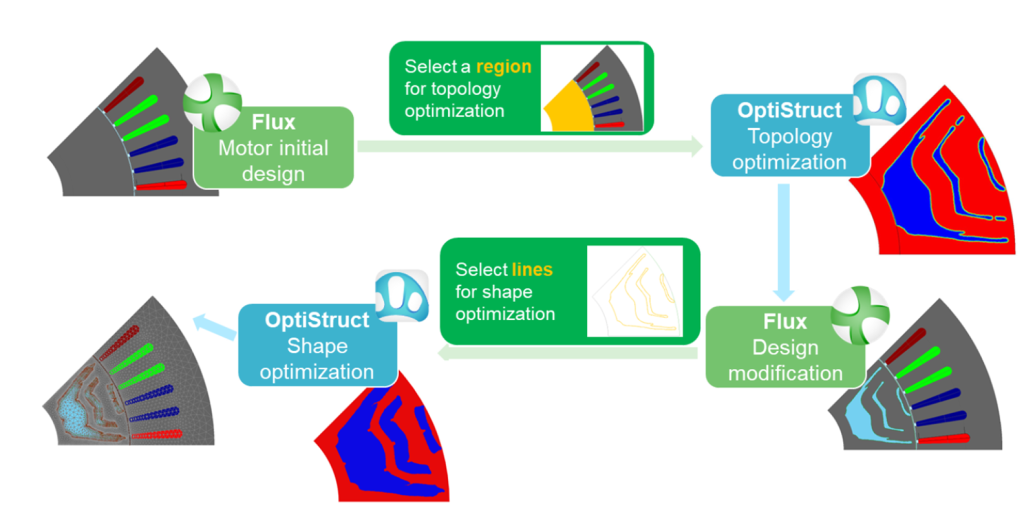
Prediction of magnetic losses and irreversible demagnetization
One of the most critical problems in permanent magnet machines is the irreversible demagnetization, a phenomenon that especially occurs at high temperatures. The demagnetization can significantly affect the machine performances, reducing the power and the overall efficiency. The artificial intelligence has been successfully used to predict and to prevent this phenomenon, combining FEM simulations with predictive models that allow identifying demagnetization risks before they take place.
Furthermore, the introduction of hybrid magnet configurations has contributed in reducing the demagnetization risk. The use, for instance, of a combination of magnets made of rare earths and ferrites in the least stressed areas has allowed improving the machine performances, meanwhile decreasing the overall cost of materials. This type of innovation has paved new ways for the design of more resistant and sustainable electrical machines, able to operate under high temperature and stress conditions without affecting performances.
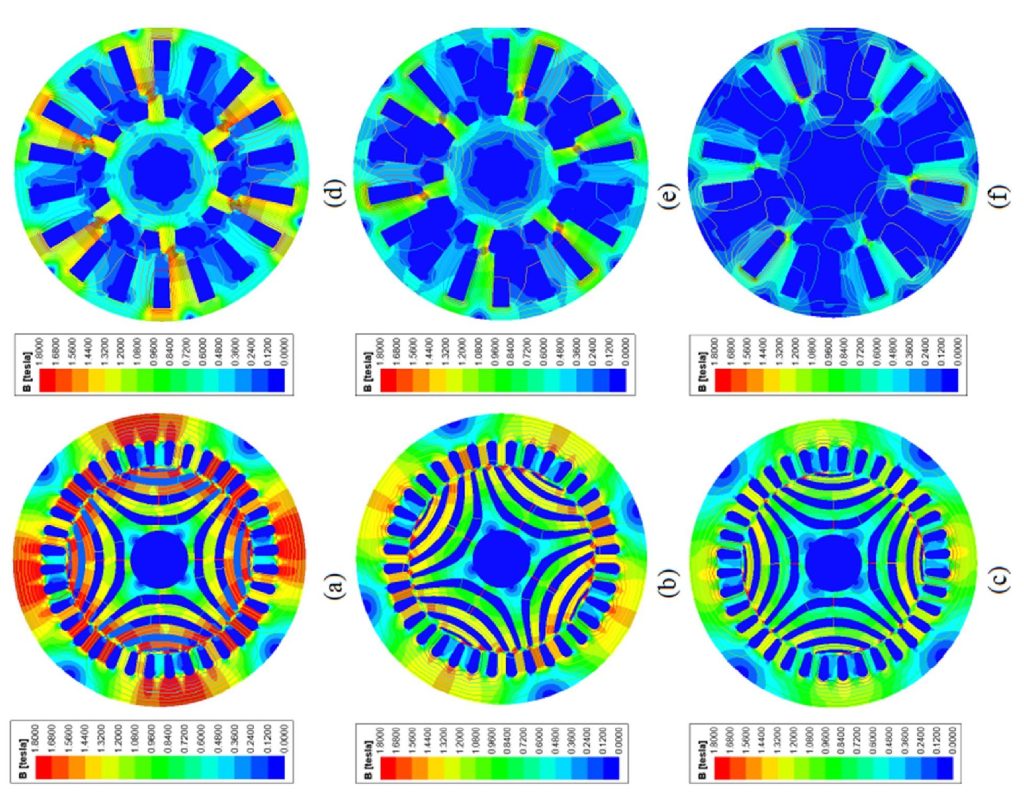
Problems connected with the design of electrical machines
The design of electrical machines issues several technical challenges, especially when we try optimizing performances in presence of constraints such as space, materials and costs. Among the most common problems, we can find the management of unbalanced electromagnetic pulls (UMP) and the need of reducing the torque ripple.
The rotor eccentricity is one of the primary causes of unbalanced electromagnetic pulls (UMP) in electrical machines, in particular in permanent magnet synchronous machines (PMSM). The rotor eccentricity causes a non-uniform distribution of the magnetic field, generating vibrations and noise that can decrease the operational efficiency and affect the machine service life.
Recent studies have demonstrated that the use of eccentric magnets can significantly decrease the UMP, improving the machine stability and reducing the problems connected with noise and vibrations. FEM simulations are essential to assess the effects of the rotor eccentricity and to optimize the configuration of magnets to assure a more stable and efficient operation. Moreover, the use of predictive models based on the artificial intelligence allows anticipating UMP problems and correcting the design before manufacturing, improving the quality and the reliability of electrical machines.
Optimization for the reduction of the torque ripple
Torque ripples are another common problem in electrical machines, in particular in Ring Winding Axial Flux Permanent Magnet Machines (RWAFPM). The torque ripple causes undesired variations in the machine motion, negatively influencing the control quality and decreasing the overall efficiency. To reduce the torque ripple, geometrical optimization techniques are used, such as the chamfering of magnetic poles, which allows improving the torque profile and decreasing vibrations.
The optimization based on Design of Experiments (DOE) is another efficacious approach to solve the problems connected with the torque ripple. This method allows exploring a broad range of design configurations, reducing the computational complexity and quickly identifying the most promising solutions. In this way, it is possible to optimize the design of electrical machines, assuring high performances and a fluid operation in a wide range of operational conditions.
The use of new materials and configurations
Besides the above-described problems, the innovation in the design of electrical machines is also focusing on the use of new materials and configurations to improve performances and to decrease costs. The design optimization of permanent magnet machines, for instance, includes the development of new hybrid configurations that reduce the use of rare materials, maintaining high performances. In this context, the optimization of Ring Winding Axial Flux Permanent Magnet Machines (RWAFPM) has been particularly efficacious.
Furthermore, in synchronous reluctance machines (SynRM), the magnetic flux optimization through the use of AI techniques has permitted to improve the energy efficiency and to reduce magnetic losses. The forefront cooling configurations, such as the oil cooling and thermal exchange systems, contribute in keeping operational temperatures optimal, improving performances without affecting the reliability.
In brief
The integration of the artificial intelligence and of advanced optimization techniques is revolutionizing the sector of electrical machines. AI allows significantly shortening design times, meanwhile improving performances and reducing costs. Innovations in design, like the hybrid configurations of magnets and the geometrical optimization, are improving the energy efficiency and reducing the problems linked with physical phenomena such as the irreversible demagnetization and unbalanced electromagnetic forces.
The electrical machines optimized by using the AI represent the future of the sector, permitting to reach unprecedented levels of performance and sustainability. The advanced simulation and optimization techniques permit to face more complex design challenges, assuring more efficient, sustainable and performing machines in a broad range of industrial applications.
(by Andrea Mura, Department of Mechanical and Aerospace Engineering, Politecnico di Torino)